Laser spot welding using NdYAG laser system
Theory
Prerequisite
For better understanding of the experiment a candidate should acquire following knowledge
- Basic knowledge of LASER
- Laser formation and important terminologies
- Various input parameters and their significance
- Orthogonal array, Design of experiments
Laser spot welding [3, 4]
Advances in manufacturing technology and the trends for smaller part geometry have opened the door for new metal-joining applications where traditional TIG and resistance welding methods no longer meet precision, quality, or productivity requirements. Pulsed Nd:YAG laser spot welding technology is now being used to replace these processes, often with increased productivity and lower overall cost.
Moreover, the demand for greater precision in high-performance assemblies has favoured the use of these lasers as a more cost-effective alternative to the resistance welding that has been used for decades. Nd:YAG laser spot welding eliminates problems associated with resistance welding, including electrode sticking, and cleaning or replacement. Also, since laser welding is a non contact process, there is no metal deformation of the component parts. Spot welding is the simplest form of laser welding. There are two types of spot welding modes: conduction and penetration. The conduction welding mode is employed for micro-joining purposes. Penetration welding permits aspect ratios (ratio of depth to width) much higher than unity. Related to the process are parameters such as the welding speed, the focal length of the beam, focusing lens, the work piece position relative to the beam focal point and the shielding gas type and flow characteristics.
There are some conditions, though, which must be satisfied in laser spot-welding:
- Highly accurate positioning of the components to be welded.
- Accurate positioning of the components in the focus of the laser to prevent large variations in the irradiance.
- Creation of a protective atmosphere.
- Symmetrical laser welding
The majority of laser spot welding applications use parts made of galvanized low carbon 1010 and 1100 cold-rolled steel along with 304, 306, and 400 series low-carbon stainless steel, ranging in thickness from o.41 to 1.57mm. The effects of spot welding on these common materials are well known and documented.
Many manufacturers of automotive components are introducing pulsed Nd:YAG lasers for precision spot welding application. Some battery manufacturing are using nickel tabs for spot welding of the interior and exterior of the battery in order to provide electrical contact and mechanical strength without thermal damage or deformation of the components [3].
1.0 Process Mechanisms There are two modes of welding with the laser as given below
- key welding
- conduction welding
1 Keyhole welding
The power density available from an industrial laser beam spans many orders of magnitude, attaining 106 W/mm2 in a high quality focused beam. However, such a high power density is difficult to control, and keyhole welding is normally carried out with a power density on the order of 104 W/mm2. The surface of the material vaporizes at the point of interaction. The recoil force of vaporization from the liquid surface causes a surface depression, which develops into a deeply penetrating vapour cavity by multiple internal reflection of the beam, as illustrated in Figure 1.10 [2], the diameter of keyhole is approximately equal to that of the beam diameter.
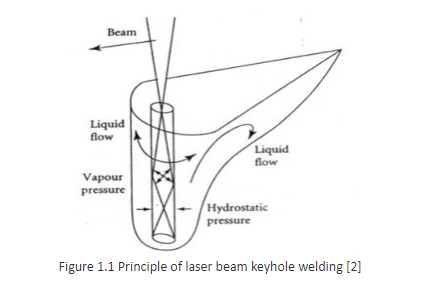
Energy is absorbed by the material through two mechanisms, which determine the overall energy transfer efficiency. Inverse Bremsstrahlung absorption (transfer of energy from photons to electrons) takes place in the partially ionized plasma formed in and above the keyhole; it is the dominant mechanism at low welding speeds. Fresnel absorption by multiple reflections at the walls of the keyhole dominates at high welding speeds, and is dependent on the polarization of the beam. Plasma (ionized vapour) and plume (vaporized material) facilitate energy transfer from the beam to the material, but they also defocus the laser beam, reducing its power density.
The vapour cavity is surrounded by molten material. The cavity is maintained through equilibrium between opening forces arising from material ablation and plasma formation, and forces caused by the surface tension and hydrostatic pressure of the molten pool, which act to close it. As the beam and material move relative to one another, material is progressively melted at the leading edge of the molten pool and flows around the deep penetration cavity to the rear of the pool where it solidifies in a characteristic chevron pattern. The requirement to maintain this balance leads to practical minimum and maximum traverse rates for keyhole welding- excessive speed causes the keyhole to collapse, whereas insufficient speed results in a wide weld bead that sags. The shape and size of the keyhole fluctuate during welding. The molten pool temperature is considerably higher than that of a conventional arc weld. Heat is conducted into the surrounding material to produce a narrow HAZ as shown in Figure 1.2 [4]. When the laser beam is turned off, several processes occur: the plasma inside the keyhole is extinguished; vaporization pressure decays; and the keyhole collapses through the effects of surface tension and gravity.
Keyhole weld exhibits two distinct regions: a fusion zone; and an HAZ. Within the HAZ, sub regions can be identified; their extent depends on the material composition and the peak temperature attained during welding. The relationship between microstructure and peak temperature is illustrated for a structural steel weld in Figure 1.3[2]. Each region has specific composition, microstructure and set of properties.
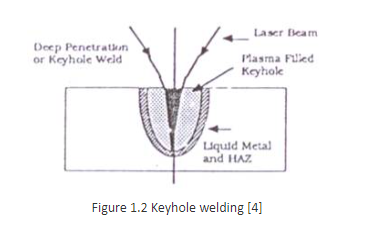
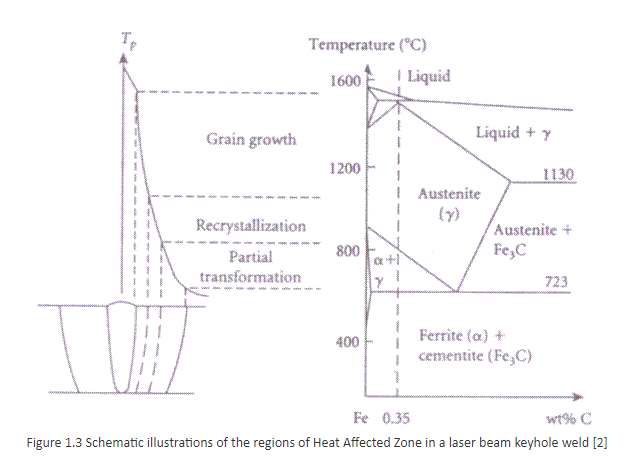
1.2 Conduction welding [2, 4] Conduction joining describes a family of processes in which the laser beam is focused to give a power density on the order of 103 W/mm2, which is used to fuse material to create a joint without significant vaporization. Conduction welding may be performed in two modes: direct heating; and energy transmission. During direct heating, heat flow is governed by classical thermal conduction from a surface heat source and the weld is made by melting portion of the base material. Transmission welding is an efficient means of joining polymers that transmit the near infrared radiation of Nd:YAG and diode laser; energy is absorbed through novel interfacial absorption method. The process parameters are determined by the material properties: higher power levels are required for materials of high thermal conductivity, high melting temperature and low absorptivity.
However, many of the procedures and properties of conduction welded materials are similar to those of keyhole welding. At low power density, the melt puddle depression does not occur and the laser energy input creates a smooth shallow liquid pool. This pool will grow in size until the laser energy delivered into the puddle equal the energy lost to conduction into the rest of the solid metal. Upon solidification of the puddle, a cross section of the parts will show a weld that has a penetration no greater than half the width of weld. The surface of the weld is very smooth and cosmetic because the melt puddle is not recoiling during solidification.
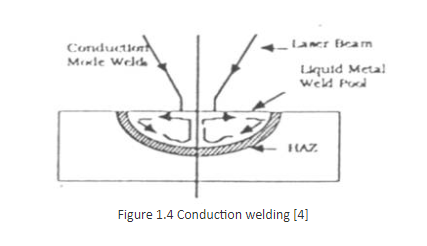
The mechanism of direct heating involves absorption of the beam energy by the material surface and subsequent transfer of energy into the surrounding material by conduction. A hemispherical weld bead and heat affected zone (HAZ) is formed in a similar manner to conventional arc fusion welding process. Conduction-limited weld as shown in Figure 1.4 [4], therefore, exhibit a low depth-to-width ratio (aspect ratio), which is often required when limited penetration in the thickness direction is desired. Thermal cycles are rapid, resulting in a fine-grained weld bed with good mechanical properties. Spot welds are made by pulsing the laser beam to melt sufficient material to form the joint.
Advantages of laser spot welding
The advantages of the laser technique, compared with arc or resistance welding processes are summarised as follows [1]:
- Low heat inputs to the materials, minimizing distortion;
- High process speed; Easily automated process;
- No weaving required;
- The only consumable is shielding gas, apart from normal laser requirements;
- It forms a narrow deep weld, small heat-affected zone;
- It can be applied in confined areas;
- Access to only one side of the material is required.
Comparison of Various Welding Processes [3]: Comparison of laser spot welding with other types of spot welding on the basis of certain welding characteristics is summarised in Table 1.1 below:
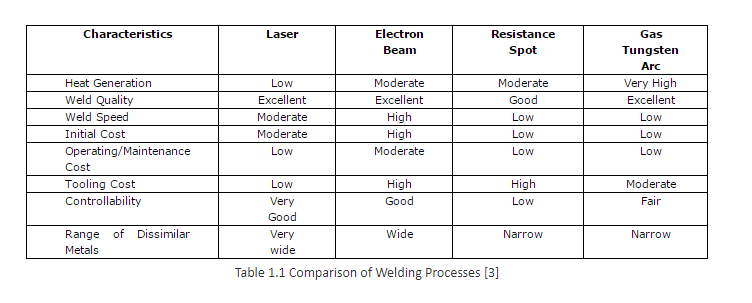
Applications of laser welding [2, 3]
There are numerous applications of laser spot welding; some of them are as listed below:
- The common industrial application of laser conduction welding, are those in which large numbers of identical small parts are joining. The examples in aerospace, automotive, biomedical, domestic goods ship building and electronics industries through the use of various micro-joining techniques.
- Laser spot welding, three pieces of a relay are welded with four weld spots, the material with a thickness of 0.3 mm and 0.9 mm, with this system, spot welds are achieved with a diameter 0.6 mm.
- Laser spot welding of car door panels, stamped muffler, floor panels.
- Computer hard drive component joined by pulsed Nd:YAG laser spot welding. Laser spot welding of a 0.05 mm diameter copper wire with polyimide coating to a 0.35 mm AISI 316 stainless steel wire for a catheter.
- Laser lap weld in a light weight structure with a pressed sheet steel corrugated core.
- Connector with a material thickness of 0.2 mm, a weld spot diameter of 0.4 mm is obtained.
- A ball race welded by eight weld spots. The material is austenitic steel and thickness of each ring is 0.5 mm.
- Spot welding razor blades, conduction welding of diaphragms and welding thick and thin steels.