Study of Rectilinear Motion 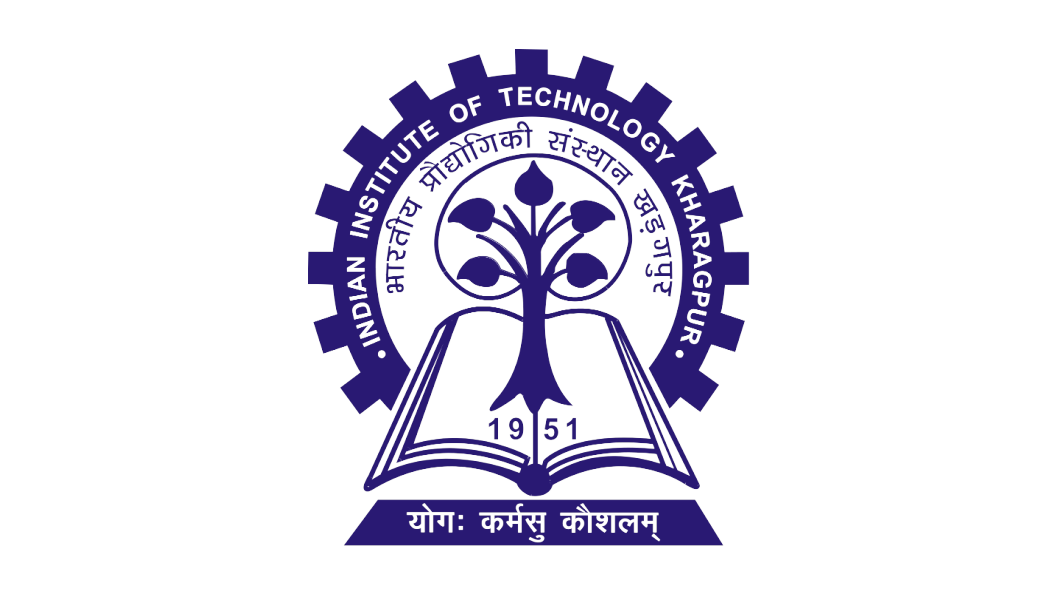
Theory
Rectilinear Motion
Rectilinear motion is another name of straight-line motion. This type of motion describes the movement of a particle or a body. A body is said to experience rectilinear motion if any two particles of the body travel the same distance along two parallel straight lines. The fig 1 illustrates rectilinear motion for a body.
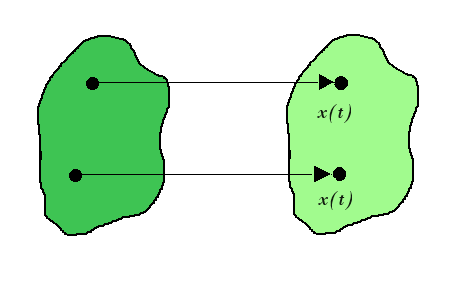
Fig. 1. Rectilinear Motion
The experimental control system in practical laboratory is comprised of the electromechanical plant which consists of the spring-mass mechanism, its actuator and sensors and a subsystem i.e. an operating program or software which runs on a PC.
Encoder
An encoder is a sensor that converts a positional output into an electronic signal. In this experiment, encoder counts are used as the system units of position, where the counts correspond to the encoder pulses and controller-internal register values. Here, 1 encoder revolution is equivalent to 16,000 encoder counts, which corresponds to 7.06 cm.
Rectilinear Motion Setup in Control Systems
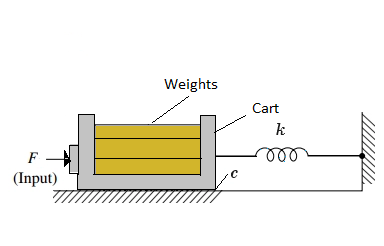
Fig. 2. Rectilinear Motion Setup without dashpot connected
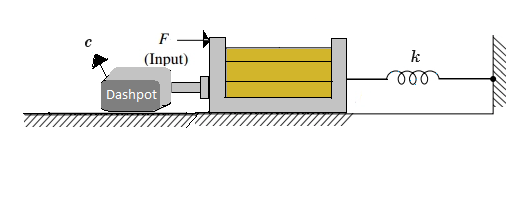
Fig. 3. Rectilinear Motion Setup with dashpot connected
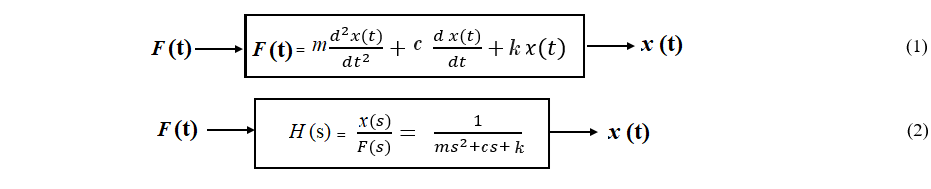
Re arranging the equation (2) and comparing the denominator terms with the characteristics equation of a second order control system we get,
$$s^2 + 2 \zeta \omega_n s + \omega_n^2 = s^2 + \frac{c}{m}s + \frac{k}{m} \tag{3}$$
$$\omega_n^{2} = \frac{k}{m} \tag{4}$$
$$\zeta = \frac{c}{2 \sqrt{k m}} \tag{5}$$
$$\omega_d = \omega_n \sqrt{(1 - \zeta^{2})} \tag{6}$$
Where,
m = Total mass (mass of the cart + weights)
k = Spring constant
c = Damping coefficient
ζ = Damping ratio
F(t) = Applied force
x(t) = Time varying position of the cart
ωn = Natural frequency of oscillations
ωd = Damped natural frequency of oscillations
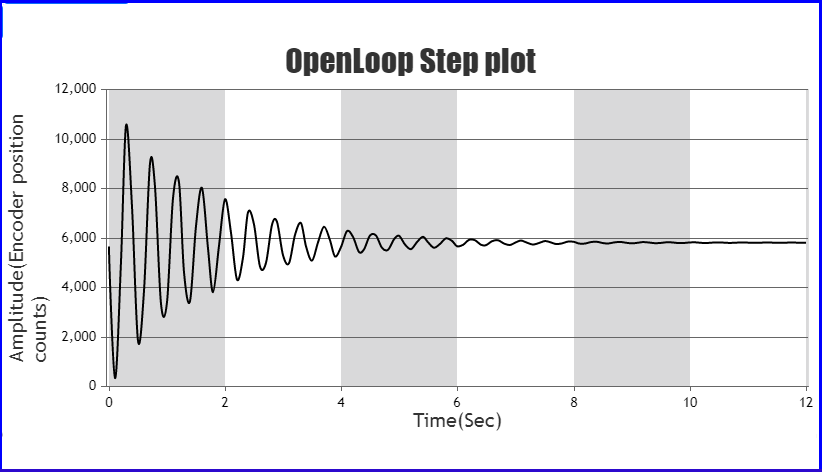
Fig. 4. Open loop step plot for 1 kg mass on Mass Spring Damper system without connecting the dashpot
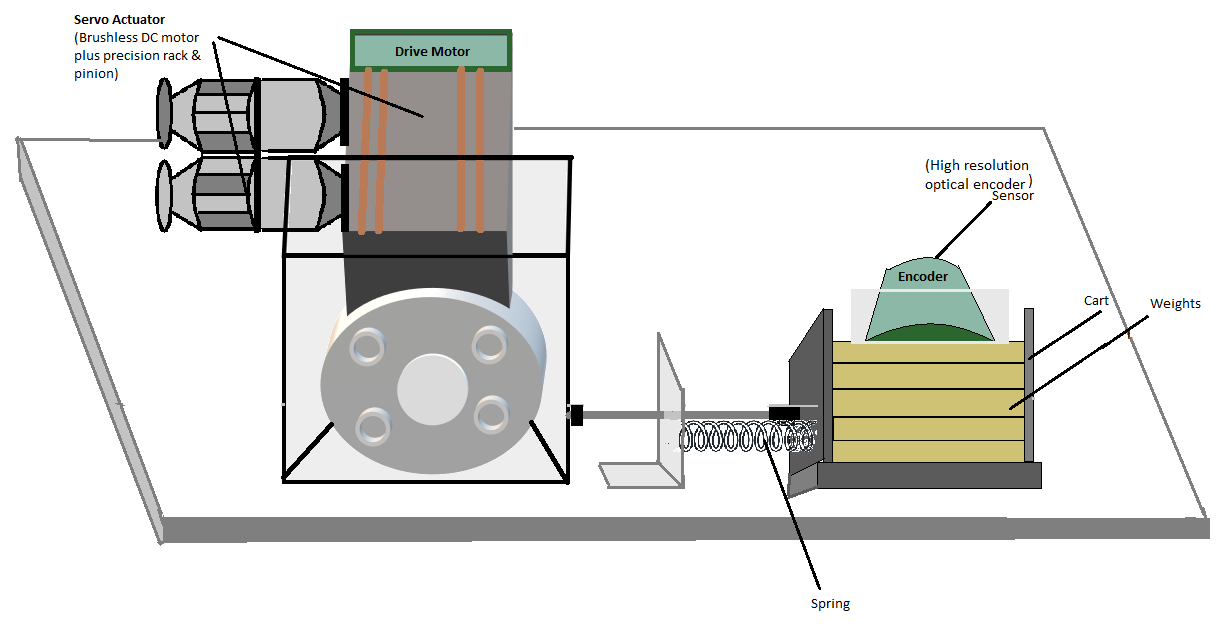
Fig. 5. Rectilinear Plant
The hardware gain, khw, of the system is comprised of the product
$$k_{hw} = k_c \ k_a \ k_t \ k_{mp} \ k_e \ k_{ep} \tag{7}$$
where the theoretical values are
kc, the DAC gain, = 10V / 32,768 DAC counts
ka, the Servo Amp gain, = approx 2 (amp/V)
kt, the Servo Motor Torque constant = approx 0.1 (N-m/amp)
kmp, the Motor Pinion pitch radius inverse = 26.25 m-1
ke, the Encoder gain, = 16,000 pulses / 2π radians
kep, the Encoder Pinion pitch radius inverse = 89 m-1