Microstructure of Various Steels (hypoeutectoid, eutectoid and hypereutectoid)
Carbon steels represent the most extensively utilized class of alloys in both industrial applications and daily use. As delineated in the iron–carbon phase diagram (Figure 1), compositions containing less than 2.1 wt% carbon are classified as steels, whereas compositions ranging from 2.1 wt% to 6.7 wt% carbon fall within the cast iron domain. The upper compositional limit at 6.7 wt% carbon corresponds to the formation of cementite (Fe₃C), an intermetallic compound with an orthorhombic crystal structure.
Figure 1. The Iron Carbon phase diagram
The steel region of the iron–carbon phase diagram includes important phase transformations that govern the heat treatment and microstructural evolution of steels. The following are the details of these main reactions.
Eutectoid Reaction: The eutectoid reaction occurs at 723 °C and 0.76 wt% carbon, where a single solid phase, austenite (γ), transforms into two distinct solid phases: ferrite (α) and cementite (Fe₃C). This reaction is represented as:
γ→α+Fe3C
It is a critical transformation in steels, producing a characteristic lamellar microstructure known as pearlite, which consists of alternating layers of soft ferrite and hard cementite.
Peritectic Reaction: The peritectic reaction occurs at approximately 1493 °C and 0.17 wt% carbon, within the low-carbon steel region. It takes place during solidification and involves a liquid phase (L) reacting with solid δ-ferrite (δ) to form austenite (γ), as represented by:
L+δ→γ
This is a solid–liquid → solid transformation occurring over a narrow composition and temperature range. The peritectic reaction is diffusion-controlled and often incomplete during rapid cooling, which may result in microsegregation.
Austenite–Ferrite Phase Transformation: This solid-state transformation occurs over a range of temperatures depending on the carbon content. In the iron–carbon phase diagram, it takes place between 910 °C and 723 °C for compositions up to 0.76 wt% C, and is represented as:
γ↔α
Austenite (γ) is a face-centered cubic (FCC) phase stable at high temperatures, while ferrite (α) is a body-centered cubic (BCC) phase stable at lower temperatures. As steel cools, austenite transforms into ferrite in hypoeutectoid compositions (< 0.76 wt% C), starting at 910 °C. This transformation progresses down to the eutectoid temperature of 723 °C and is driven by diffusion, involving carbon redistribution and a change in crystal structure.
Austenite–Cementite Phase Transformation: This transformation occurs in hypereutectoid steels (0.76–2.1 wt% C) as the alloy cools below the solvus line (Acm). In this process, austenite (γ) decomposes to form cementite (Fe₃C), a hard and brittle iron carbide. The transformation begins just below the Acm temperature and continues until the eutectoid temperature (723 °C), at which point the remaining austenite transforms into pearlite. The microstructure features proeutectoid cementite precipitated along grain boundaries, which increases hardness but may reduce toughness. Careful control of this transformation is crucial for optimizing the mechanical properties of high-carbon steels.
In the Fe-rich region of the iron–carbon phase diagram (Figure 2), several key phases are observed: austenite (γ), ferrite (α), and cementite (Fe₃C). Austenite has an FCC crystal structure and is stable up to a maximum carbon solubility of 2.11 wt% at approximately 1150 °C. Its stability range includes the eutectoid point at 0.76 wt% C and 723 °C, where it exhibits a minimum in the phase boundary.
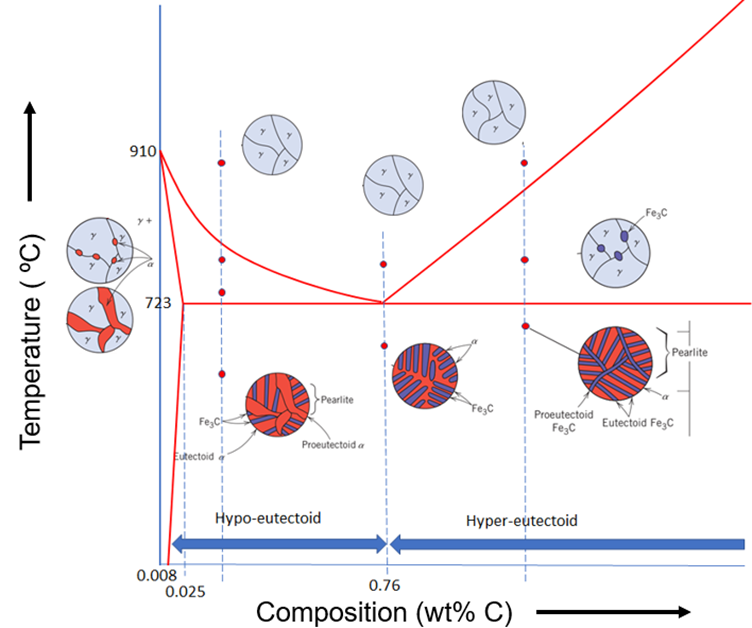
a.
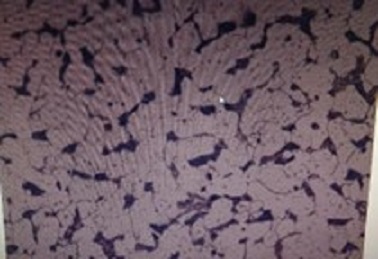
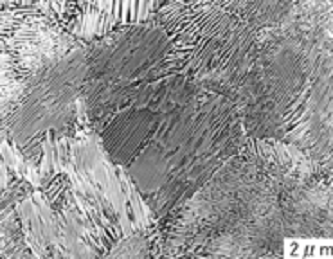
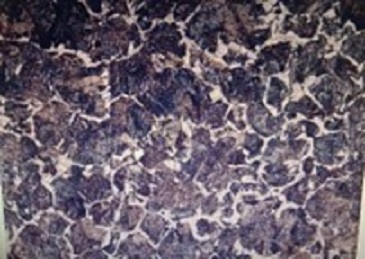
When an alloy with a composition near 0.8 wt% C is cooled below 723 °C, austenite undergoes a eutectoid transformation, decomposing into ferrite and cementite simultaneously. This diffusion-controlled process results in the formation of lamellar pearlite colonies (as shown in Figure 3(c)).
Hypoeutectoid steels, which contain less than 0.8 wt% carbon, exhibit a microstructure consisting of proeutectoid ferrite and pearlite. Upon cooling from the austenitic region, ferrite begins to precipitate first, especially along prior austenite grain boundaries. As the temperature decreases, the remaining austenite becomes enriched in carbon until, at 723 °C, it transforms into pearlite (shown in Figure 3(a)). The proportion of ferrite increases as the carbon content decreases.
In contrast, hypereutectoid steels (carbon content > 0.8 wt%) show a microstructure of proeutectoid cementite and pearlite. During cooling, cementite precipitates first along the austenite grain boundaries. Upon reaching 723 °C, the remaining austenite transforms into pearlite, as shown in the electron micrograph in Figure 3(c). As the carbon content increases, the volume fraction of cementite also increases, leading to greater hardness but potentially reduced ductility.